Casque Felin maison: 4- Joncs & Plaquettes
Fabrication d'un casque Felin maison d'airsoft d'après photos.
CASQUE FELIN- AIRSOFT MAISON
4- Joncs & Plaquettes
4ème étape: travail d'impression 3D pour les joncs et les plaquettes.
Pour la modélisation des garnitures et des plaquettes du félin home-made, il va falloir scanner mon casque modèle comme je l'ai fait pour le mich. Cliquez sur ce lien pour plus de détails: Pseudo Felin sur Mil-Tec non modifié
4.1- Scannage de la coque
Si la couleur est unie, la mise au point de l'APN est parfois difficile voir impossible. J'ai testé sur mon modèle tout gris bien lisse, je faisais à peine une mise au point sur 10 essais grand max.
Du coup j'ai tacheté le modèle, un peu de pshhht avec des bombes de peintures et un peu de taches à coup de tamponnage avec une brosse à dents (un pinceau aurait très bien fait l'affaire, je voulais passer mon doigts sur la brosse histoire de balancer des gouttelettes mais après réflexion, je me suis dit que j'allais me salir, du coup j'ai juste tamponné).
NB: la prochaine fois que j’essaie, je mettrais juste des coups de tampons rond et nettes pour voir. Car après tout, c'est juste une question de mise au point de mon apn là. Et je ne sais pas si ça compte vraiment pour le scannage.
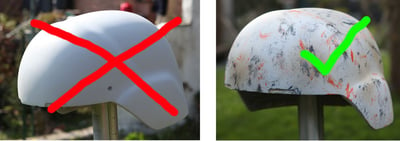
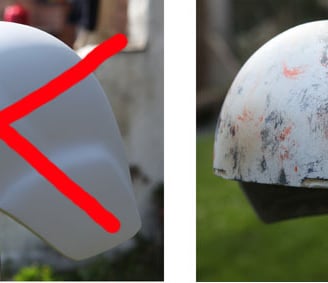
Bref 439 photos plus tard, passage dans MeshRoom pour le scannage 3D, calcul de l'ordi pendant plusieurs heures et j'ai mon modèle en centaines de milliers de polygone avec un bout d'herbe et de trépied.
Puis un tour dans MeshMixer pour "détourer" le casque (retirer le trépied et l'herbe), orienter approximativement sur les 3 axes le casque et surtout le mettre à l'échelle.
Cette fois, je n'utilise pas MeshLab pour simplifier et essayer de transformer en quadmesh vu que ça ne marche pas. Je passe donc directement sur Fusion360.
Voilà, c'est prêt pour la modélisation.
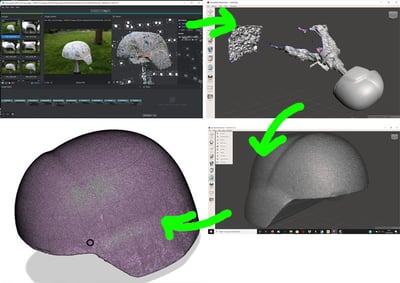
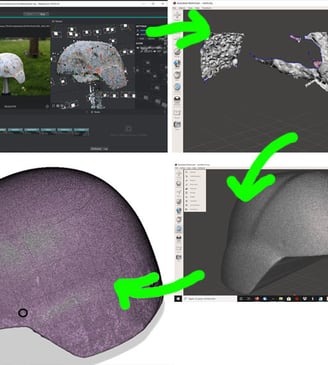
4.2- Garnitures
J'ai appelé "garnitures" les "joints" en bordure du casque, qui sont le plus souvent appelés "joncs". Mais bon, à l'époque, j'ai trouvé plus judicieux d'appeler ça "garniture".
Sur le vrai, ce sont des pièces en plastiques, comme les plaquettes sur les oreilles. Et non pas un joint souple en forme de "U" comme sur ma réplique de mich.
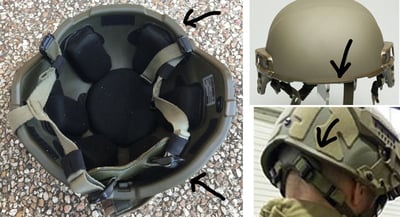
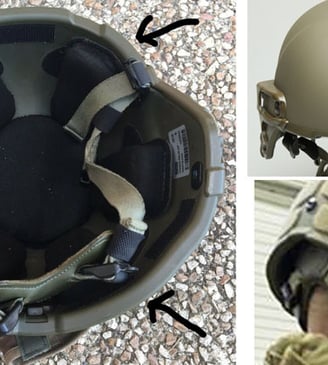
4.2.1- Garniture Frontale
On va commencé par celle à l'avant. Comme j'ai eut accès à un vrai casque, j'en ai profité pour faire des mesures.
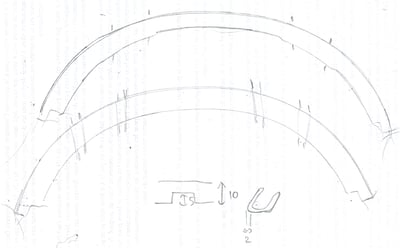
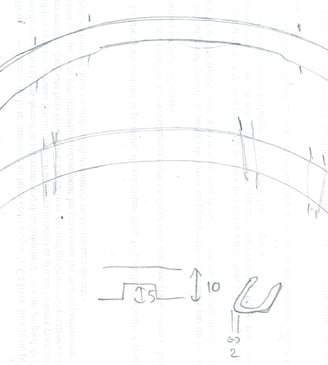
Comme vous pouvez le voir, l'avant du casque a une forme très "plate" et pas du tout "arrondie" comme sur un mich ou un ops-core.
Le profil est prévu pour le montage de la griffe lucie et autres bidules comme la vision déportée. Mais il parait que c'est aussi pour limiter la prise au vent lors du parachutage.
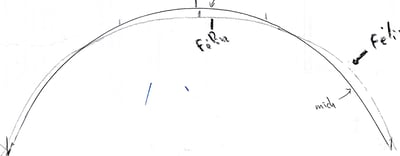
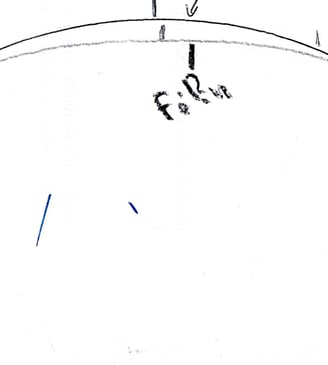
1er crobar: j'ai fait varié les épaisseurs de plastique selon la localisation. Le dessous, vers l'avant, étant la zone qui risque le plus de subir des chocs, c'est elles qui sera la plus épaisse du coup.
Par contre il s'avère au final qu'il sera inutile pour mon modèle home-made.
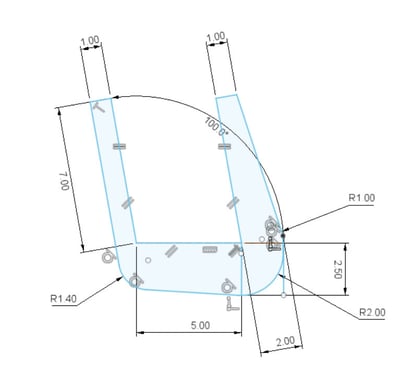
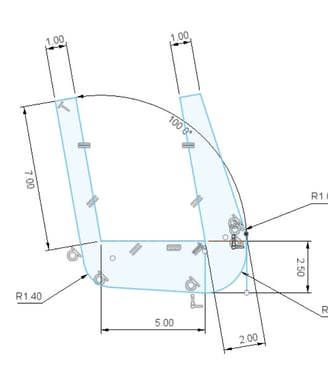
Bon vu que j'ai fait le front de mon casque en 3D, j'ai simplement utilisé ce dernier pour faire ma garniture frontale.
Sur ma modélisation j'ai un angle quasi nulle (angle droit) sur le front, du coup j'ai redessiné le truc à façon.
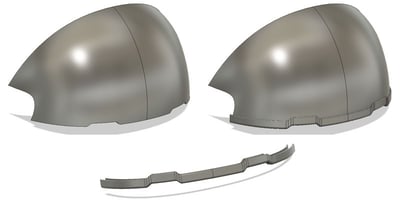

Plus qu'à l'imprimer et le tester pour voir avant de tailler les extrémités.
1er test en blanc, il est trop large, j'ai trop anticiper la déformation. du coup j'ai retracé sur une feuille de papier ma courbe, scannage de la photo, importation dans fusion et comparatif pour l'avoir plus précis.
De plus j'avais prévu 5mm de largeur (estimation de l'épaisseur de ma coque résine. Au final je suis à 4mm de moyenne. Ça descend parfois à 3mm et les grosses épaisseur font 6mm. Du coup j'ai aussi élargit la garniture. Elle fera environ 9.5mm (contre 11.2mm pour la vraie).
Du coup, mon 2ème test était presque bon (en noir). Sauf sur la longueur, je peux encore le réduire un poil.
Après encore un petit réglage de longueur et des réduction de largeur aux extrémités, le modèle fut rapidement finalisé.
La réduction aux extrémités, c'est histoire de ne pas gêné le harnais, plus exactement le glissement des sangles de réglage de la mentonnière. Comme sur le vrai casque.
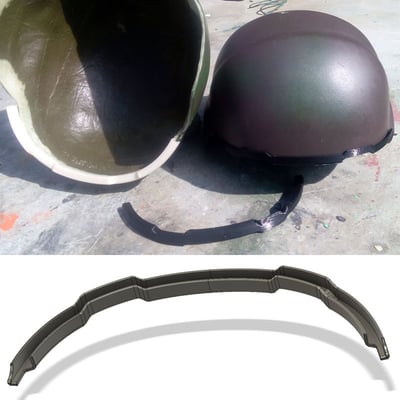
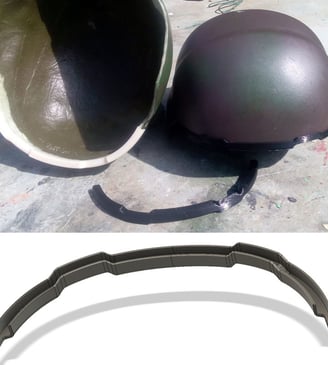
4.2.2- Garniture arrière
Un peu plus chiant à modéliser. Comme c'est une symétrie de forme à "main levée que j'ai fait sur mon modèle en résine, c'est loin d'être parfait. Pour être dans la perfection, j'aurai du faire comme à l'avant: faire une partie en impression 3D. Mais à l'arrière, il n'y a rien de notable, donc j'ai eut la flemme mais je le paye maintenant.
Mon 1er test a révélé plusieurs défaut dans la forme, jusqu'à presque 3mm entre la garniture et le bord de mon casque!
Je vais modéliser une 2ème garniture de test avec des points de repères histoire de pouvoir repérer avec précision justement les zones à retravailler au besoin.
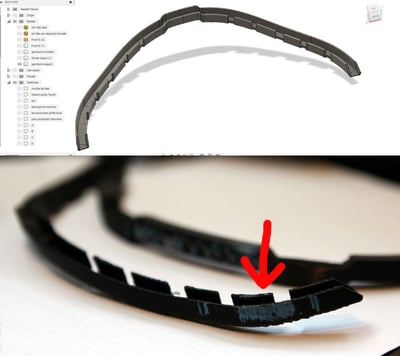
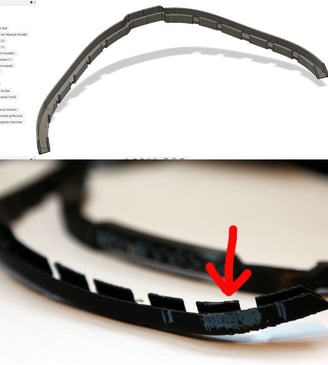
Au final j'aurais fait pas mal d'essais pour arriver à un truc propre. La modélisation de la courbe, le chemin à hauteur variable, la réorientation du profil, le repérage des zones à modifier. Mine de rien j'en ai chier sa maman. Une semaine à redessiner le bouzin tous les jours.
Mais ça y est, c'est finit.
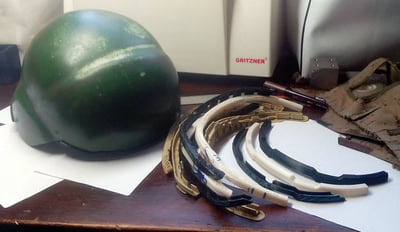

4.3- Plaquettes Felin
Les noms pompeux officiels que j'ai trouvé pour ces plaquettes sont "pièces supports des éléments missionnables" ou "pièces support de fonction FELIN AF".
Elles, j'aurais bien sur besoin de la modélisation 3D de mon modèle comme je l'avais fait pour le mich.
Donc modélisation d'une partie de coté avec l'oreille et test sur le casque pour voir si c'est bon.
Puis, comme pour le mich, test pour voir les angles etc.... Cette fois, j'imprime des aides directement pour aller plus vite. Ici, un test pour voir tout de suite si je suis aligné avec incrément de 2.5°. Bon, j'ai déjà bien orienté la face, pas de soucis. Sur ce 2ème test j'ai aussi augmenté mon modèle à 102% pour bien couvrir les bords du casque. A 102% pas de soucis, le modèle suit encore très bien la forme du casque. J'ai juste mon trou de perçage décalé de 2mm.
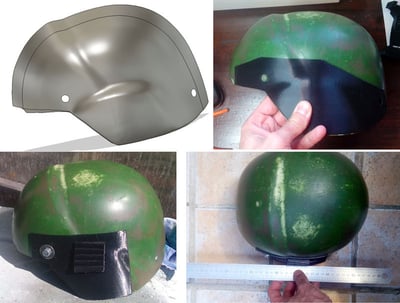
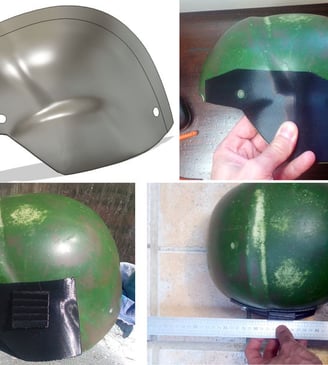
Un 2èmee test pour l'inclinaison, histoire d'être aligné horizontalement et vérification du centrage du trou.
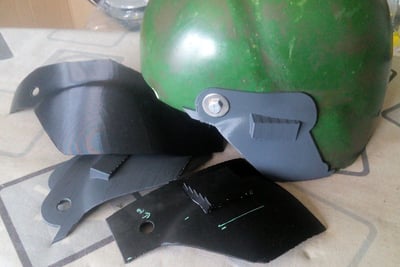
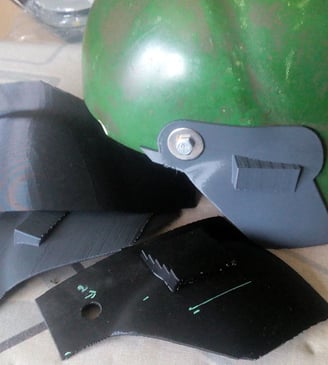
Voilà, c’est prêt. Plus qu'à remodéliser ça bien comme il faut.
La forme de l'oreille étant bien plus proche de l'original que celui du mich, j'ai entièrement redessiner la plaquette. Ça m'a pris un temps fou mais le résultat est là: elle est très très proche de l'originale au niveau de la forme et j'ai poussé le vice très loin dans les détails.
Du coup après quelques ajustages de liaison des garnitures, je suis arrivé à ce modèle final.
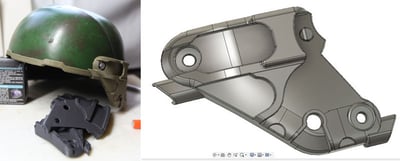
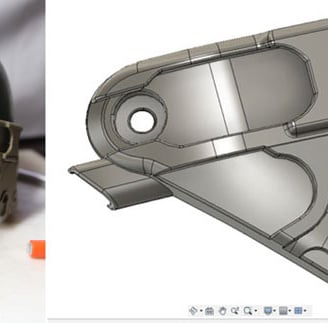
Et le résultat quasi finale est là (encore 2-3 détails d'ajustement et je serais bon :)
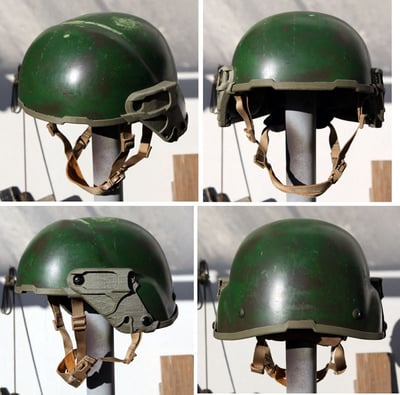
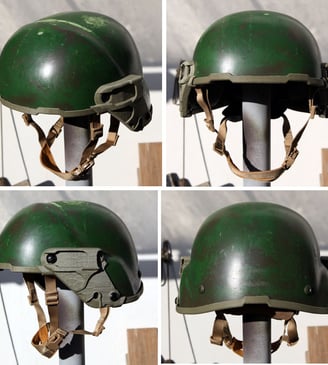
Voilà le modèle finalisé à 100%
Plus qu'à jouer les apprentis experts en impression 3D maintenant.
Bien choisir sa température, le positionnement pour l'impression pour un rendu qui me convient, le temps d'impression pas trop long....

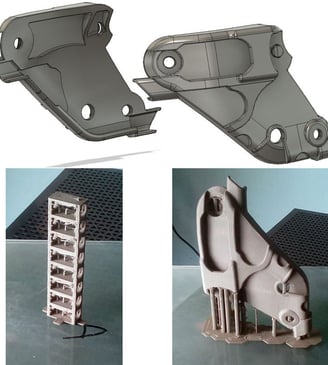
Une fois à peu près satisfait, je ponce et je lime. Je gratte, je coupe et je polis au cutter. Et je ravive la couleur au chalumeau.
Ensuite ma planche à clous, pour maintenir les impressions en hauteur pour pouvoir peindre en une seule fois.
J'ai fait un mélange avec de la peinture pour figurine (Vallejo Game Color, censément très résistante aux manipulations) et j'ai appliqué un coup de vernis satiné en bombe, car sur le vrai, le plastique fait satiné. Par contre ce n'était pas une super idée sur de l'impression 3D, les reflets brillants accentuent le relief en escalier/ par couche.
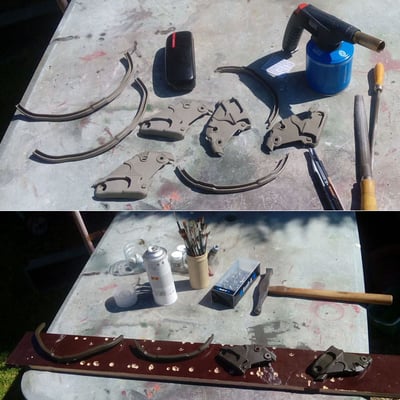
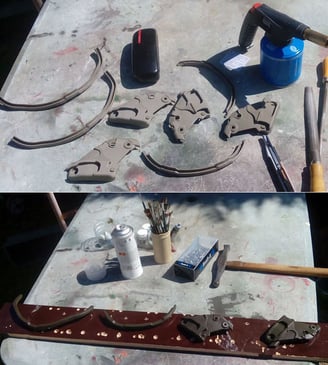
4.4- Choix des Impressions 3D
4.4.1- PLA coloré
Entre 2 j'ai reçu mes échantillons de chez ColorFabb. Une société hollandaise qui fait du PLA à la couleur que l'on veux et sans minimum de quantité. On peut donc commander juste une bobine de 750gr si on veux. Par contre, c'est du PLA de luxe du coup, vu le prix. Mais au moins, on a la couleur que l'on veut.
J'ai pris 4 échantillons.
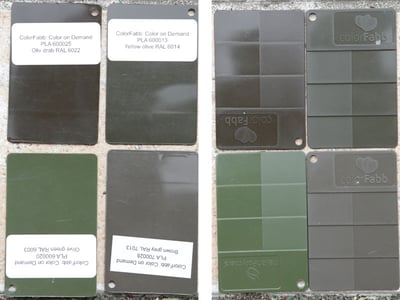
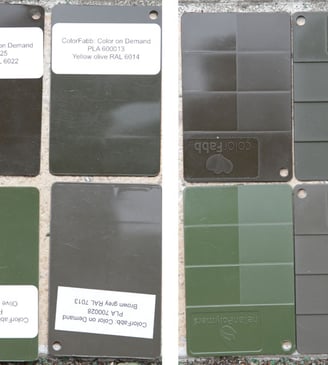
Alors si vous voulez imprimer ça vous même, ne prenez pas leur OD, RAL 6003, il est trop vert feuille/herbage. Il est trop jaune.
Le Ranger Green, RAL 7013 ressemble très fort à la couleur de la vraie griffe Lucie. Ca c'est bien.
Et le RAL 6014 est parfait pour les garnitures et les plaquettes, un bon vert OD tirant sur le marron qui dénote bien avec ma coque résine.
Le RAL 6022 est trop marron (trop de rouge). Pour les plastiques, le vrai casque est entre les échantillons du 6014 et du 6022
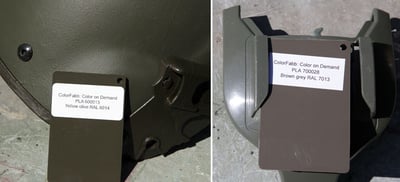
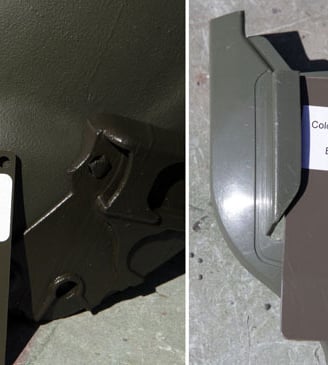
Après 15 jours, je reçoit ma bobine de 2kg. comme elle ne rentre pas dans ma machine, je me suis bidouillé un support et une manivelle que j'ai fixé temporairement sur mon établi. Tout ceci afin de rembobiner le fil sur une bobine de 1kg et de 750gr. Oui, je vais devoir vérifier ça mais leur 2 kg de PLA doit peser plus lourd que du PLA classique ou alors ColorFabb sont des arnaqueurs sur la quantité. Va falloir que je vérifie à la balance plus tard. En attendant mes bobines utilisables sont prêtes.
Enfin presque car la bobine de 2kg n'ayant pas été livré dans un emballage sous vide, je préfère sécher (avec des sels dessicants) le fil avant utilisation.
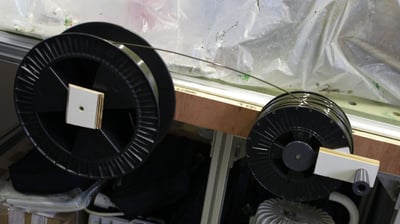
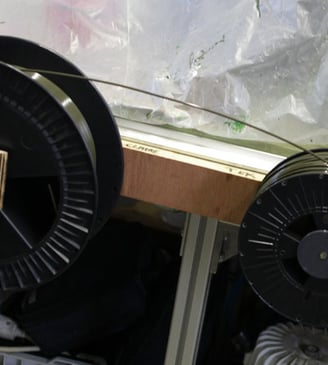
4.4.2- Impression pro
J'ai aussi reçu mon impression de chez i-materialise, j'en profite donc pour vous montrer à quoi ressemble l'impression en polyamide. Ça coute un bras par contre: comptez 90€ pour les garnitures et les plaquettes.
Impression en MJF, brut (non poli non teinté):
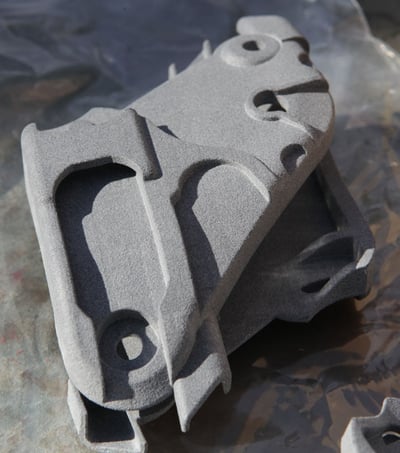
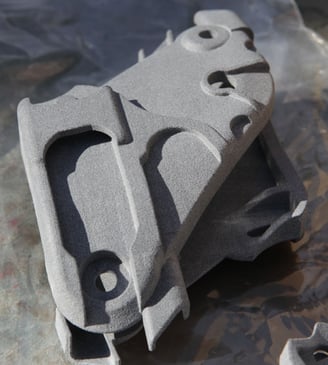
Et impression en SLS, brut (non poli, non teinté):
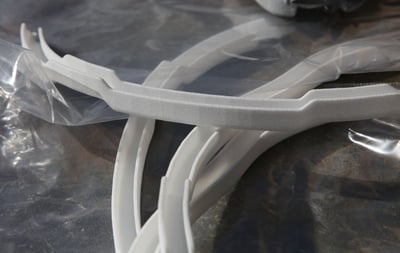
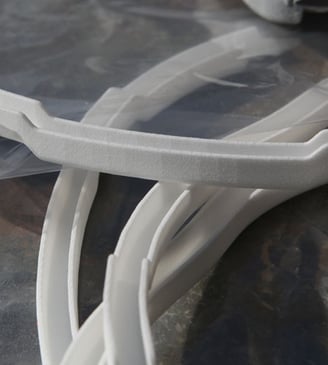
Et une fois peintes.
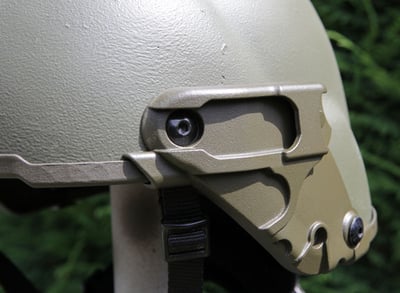
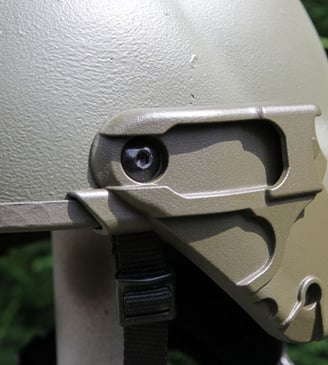
4.4.3- Comparatif avec les vraies plaquettes (edit 2021)
Comme déjà dit, si vous êtes trèèèèès patient avec MSA, vous pouvez commandé des morceaux de TC Félin.
Cf les liens ici.
Du coup j'ai acheté une paire de plaquettes. Franchement ma copie est très proche en forme de l'original. Aussi bien la coque résine que la modélisation 3D de la plaquette.
La vraie plaquette a un peu de jeu sur l'oreille.
La modélisation est très conforme à la vraie hormis les épaisseurs (adaptées pour être solide en impression 3D).
Le choix de la couleur RAL est pas mal non plus.
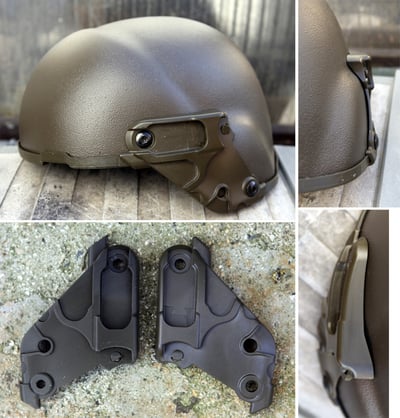
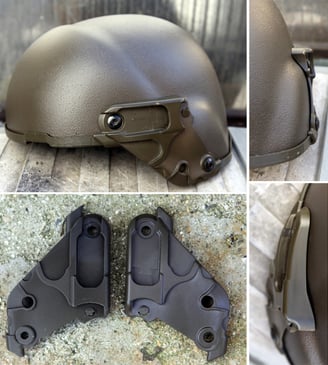
4.5- Les plaquettes modulables
Pour le Mich, il fallait une plaquette utilisable sans modifier le casque, sans devoir faire les trous supplémentaire, donc une plaquette qui risquait d'être collée. aussi il me fallait faire les rails d'accessoires amovibles obligatoirement. Mais au final, ça fait quelque chose de très gros et pas du tout low-profile.
Aussi pour ces plaquettes-ci, je vais plutôt faire de multiples plaquettes à démonter selon le système de fixation d'accessoires. Après tout, on ne change pas ça tous les jours.
J'ai commencé par agrandir l'"aileron" qui pourra servir de plateforme à "trous" de base.
Ne sachant que choisir, je vous laisse plusieurs options:

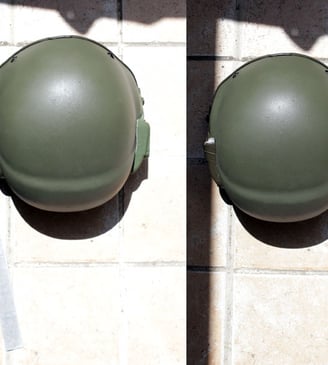
4.5.1- La version "low-profile"
Qui suit la forme de la plaquette standard. Donc l'angle de l'accessoire aussi.
Une version non perforée, à votre guise au cas ou. Une version MOE, M-LOK et KEYMLOD.
Comme ce n'est pas évidé, ce sera peut-être gênant pour serrer les écrous, mais évider la plaquette, je ne trouve pas ça esthétique non plus. Si vous avez de simples écrous hexagonaux, ce sera très certainement plus compliqué à serrer que les écrous spéciaux ovales (type écrou à souder, pour rail en T) que l'on trouve pour le M-LOK et le MOE.
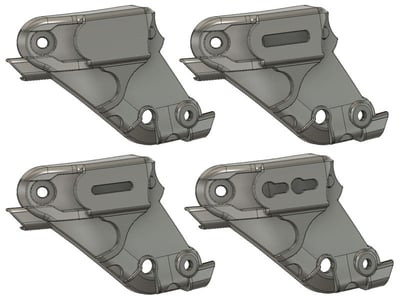
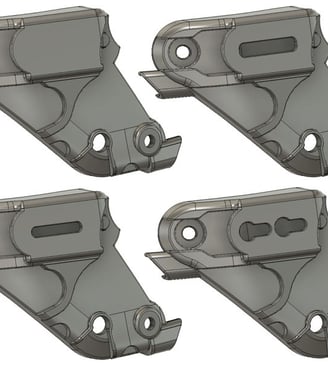
4.5.2- La version "low-profile pleine"
Une version avec plaquette évidée pour accéder à l'écrou.
Ici, je vous montre juste la version M-LOK, mais les autres adaptateurs existent aussi:
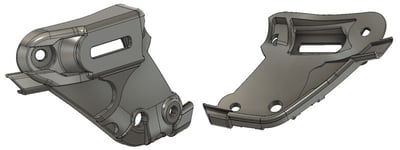
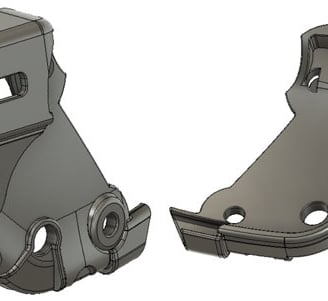
4.5.3- La version "Axe de Vue"
Une version avec plaquette évidée pour accéder à l'écrou et qui, cette fois, est dans l'axe de vue vers l'infinie. Pour les accessoires nécessitant d'être orienté dans l'axe de vue du porteur, comme une lampe pour éclairer droit devant soi.
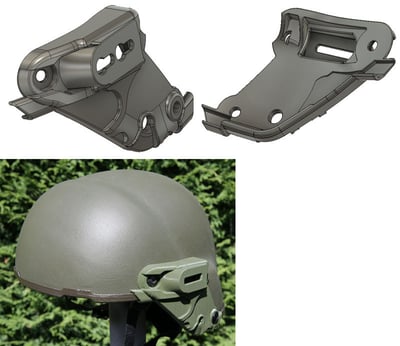
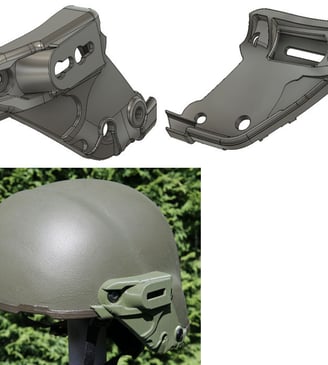
4.5.4- Le rail picatinny
Pour lui, j'ai retiré l'"aileron" pour qu'il soit moins haut. Il existe en 2 versions: "low-profile" et "axe de vue".
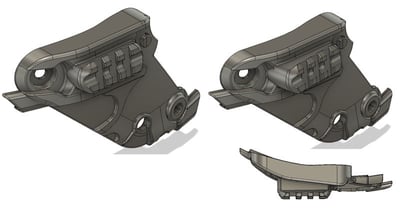
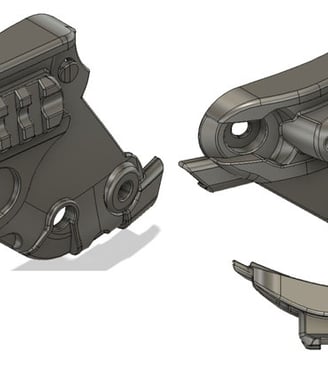
Ici un casque en version low-profile.
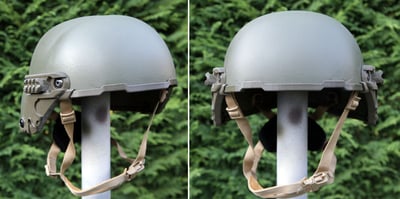
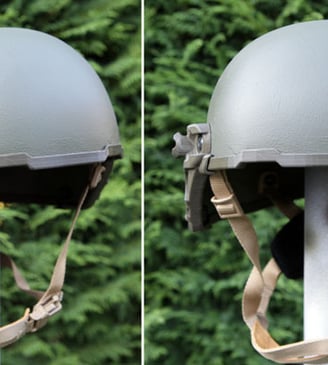
4.5.5- Le rail Ops-Core
Il n'existe qu'en une seule version, la version "axe de vue".
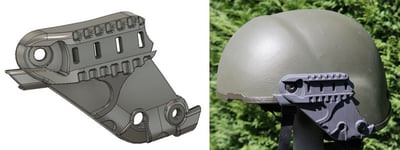
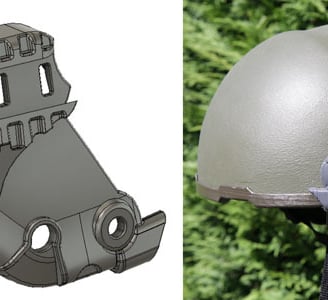
Voilà, c'est tout pour ce modèle.