Casque Felin maison: 3- Tirage
Fabrication d'un casque Felin maison d'airsoft d'après photos.
CASQUE FELIN- AIRSOFT MAISON
3- Tirages de casques en résine+fibre
3ème étape: réalisation d'un casque en résine+fibre à l'aide du moule.
3.1- Quelques essais
3.1.1- Test "Bombe de Peinture"
Un coup de peinture en bombe à l'intérieur avant d'appliquer la résine. Mon idée: la peinture sera d'autant plus solide qu'elle "fusionnera" avec la résine. Maintenant à voir si ça fonctionnera.
J'ai laissé séché la peinture environ 2-3h je pense avant de résiner.
Lors de l'application d'une 1ère couche de résine, ça a tenu sauf à l'endroit ou la peinture avait l'air de réagir. Probablement une saloperie sur l'élastomère. Peut-être qu'en nettoyant bien le moule avant application ça pourrait mieux fonctionner.
En tout cas j'ai consommé 1/2m2 de roving 160gr/m2 (le paquet complet) pour appliquer 2 couches croisées en ayant coupé le roving en bandes comme vu précédemment.
150ml de résine par couche de roving ont suffit.
Puis j'ai appliqué 2 couches de mat de verre 300gr/m2. Pareil en petites bandes. Là par contre j'ai consommé 250ml de résine par couche. Le mat apporte une épaisseur que je n'ai pas avec le roving.
En dernier lieu, j'ai mis une fine couche de gelcoat au pinceau. On dira 30ml de gelcoat par couche (intérieur puis extérieur, cf plus loin).
C'était du gelcoat blanc auquel j'ai ajouté un peu de pigment vert pour voir. Bon pour foncer le gelcoat il aurait fallut beaucoup de pigment vert, donc j'ai abandonné. D’où la couleur vert clair.
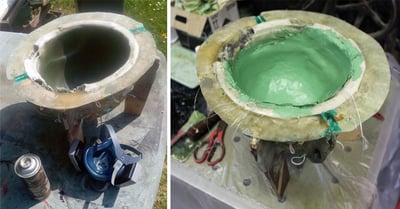
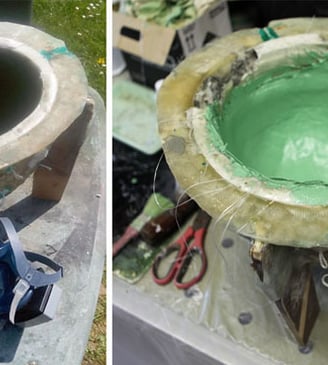
Donc 4 couches de stratifiés et 2 couches de gelcoat. En sachant qu'il faut en gros 1/2h pour poser une couche et que j’attends 1/2h mini entre chaque couche, vous comprenez que c'est assez long à faire. Et à la fin il y a encore disons 1/2h pour la découpe le temps que j'installe tout. En gros il me faut une journée pour faire un casque.
On laisse sécher 24h.
Et démoulage.
L'idée de la peinture n'est pas si mauvaise. Ça mérite d'être creusé. Notez qu'on voit bien ces non de non de bulles de merde!
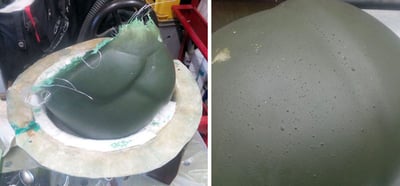
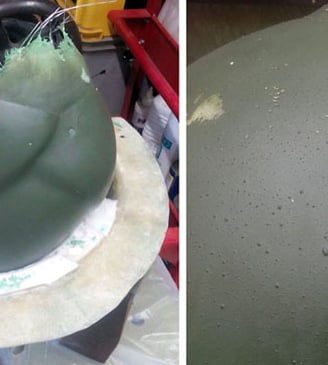
Après ponçage pour retirer les bulles/cloques, je constate que la peinture tient super bien au ponçage. C'était le but du test. Dommage qu'elle n'ait pas été homogène, j'aurai pu laisser le casque tel quel s'il n'y avait pas eut tous ces défauts.
Un coup de disqueuse, un peu de meulage puis de lime électrique pour avoir des bords bien propre à la forme.
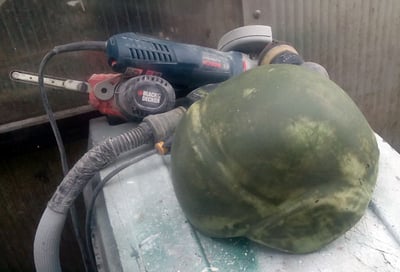
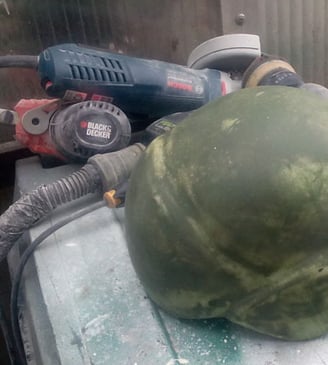
3.1.2- Test "Rouleau mousse"
Nouveau test: application du gelcoat (teinté en vert) au rouleau avec un rouleau mousse (et non à poils)
Le rouleau mousse donne un petit aspect granuleux un peu comme les vrais casques mili.
Cette fois j'ai utilisé du gelcoat transparent (environ 30ml toujours). Il est visqueux alors que le gelcoat blanc était vraiment liquide comme de la peinture. En y ajoutant du pigment vert, je l'ai liquéfié à son tour. Par contre, je n'avais plus de teinture marron universel en tube à ajouter dans le pigment vert spécial résine. Du coup, j'ai un casque qui reste couleur vert herbage, pas olive.
Sans surcharger en pigment j'ai obtenu un gelcoat opaque avec une charge d'environ 30% je dirais, donc c'est pas si mal, ça va me faire économiser en pigment.
Seul hic: le rouleau est mort après ça. Donc l'application au rouleau, ce sera quand j'aurais plusieurs casques à faire d'un coup sinon ce n'est pas économique. Déjà que le pinceau meurt très vite.
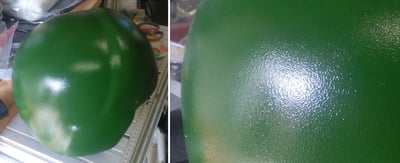
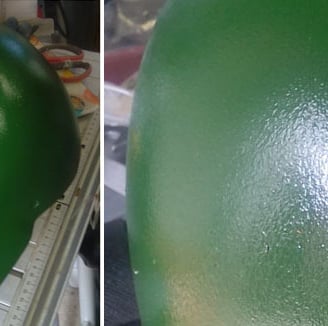
Avec le reste du gelcoat vert, j'ai fait l'intérieur du moule pour le 2ème tirage (donc l'extérieur du casque, comme pour la peinture en bombe).
Et on attend 24h pour faire sécher le gelcoat du 1er casque.
Pendant ce temps, j'ai stratifié le 2ème casque.
J'en ai profité pour faire un test de couleur.
En ajoutant du pigment universel noir et du rouge oxyde que j'avais en stock, j'ai obtenu mon vert olive militaire.
Il m'a servit à faire le gelcoat intérieur du 2ème casque.
Bon après séchage du gelcoat, ce dernier reste collant.
Le colorant universel mélangé au gelcoat réagit. Sur mes 2 essais de couleur, l'un était fort collant, l'autre moins. Il me faudra un nouvel essai en augmentant la quantité de catalyseur, je pense que c'est la solution.
En attendant, j'ai passé un coup de peinture en bombe sur le 1er casque. comme ça il ne colle plus, ça règle le problème pour le moment. Ainsi je pourrais le manipuler pour tester la griffe lucie et les garnitures qui étaient en stand-bye pour avoir les bonnes cotes.
J'aime bien le rendu du gelcoat au rouleau mousse, y'a pas, je valide le test.
Notez qu'à l'intérieur, on verra toujours la stratification de la résine, pour rappel.
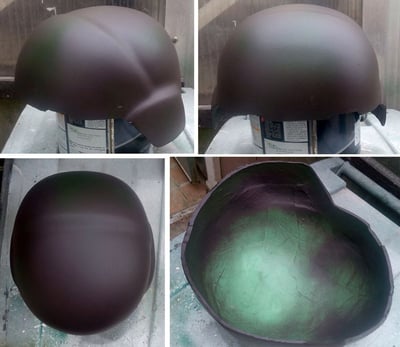
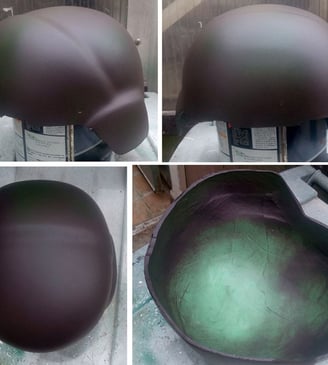
2ème casque démoulé. Pareil, il colle donc j'ai mis de la peinture en bombe pour qu'il soit sec au toucher et que je puisse le manipuler.
Alors comme précédemment, pour faire une découpe propre, je commence par découper le surplus à la meuleuse munie d'un disque à couper le métal (c'est très fin) et je découpe pas trop prêt de mon casque, histoire de ne pas manger de la matière sans le faire exprès.
Ensuite, toujours à la meuleuse, j'installe un disque à poncer et je viens enlever le surplus de matière jusque très proche de mon casque. Comme on ne peut pas être ultra précis, je laisse un peu de matière (1mm ou moins en gros).
Et la finition avec la lime électrique pour aller jusqu'à raz du casque. La lime permet de travailler précisément.
Et voilà, le casque est découpé.
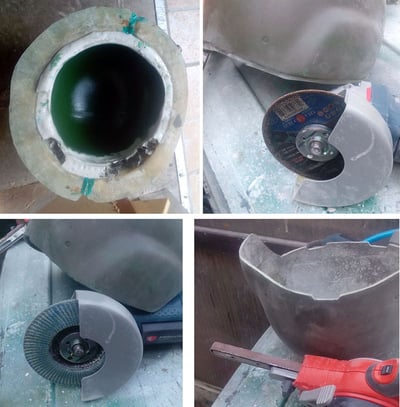
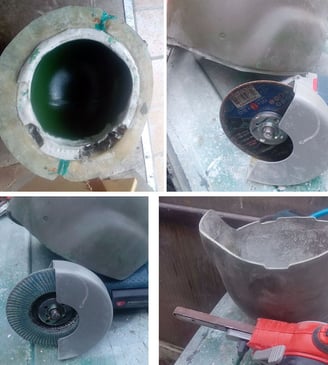
Maintenant un coup de ponçage sur ces s.... de bulles. L'étape qui n'aurait jamais du existé. Avec la lumière rasante du soleil couchant, on les voient bien sur la photo.
J''utilise un disque en mousse souple sur le plateau de ma ponceuse, ça permet de travailler en courbe. Et un un disque à poncer Abranet de chez Mirka. Des tueries ces disques à poncer. Ils sont plus cher qu'un disque classique mais on peut poncer des heures avec sans qu'il s'use. Comme c'est une trame aérée et non un disque plein perforé, il s'adapte sur toutes les ponceuses. Et dès qu'il s'encrasse, ben on tapote ou un coup de soufflette et hop, il est débouché et n'est plus encrassé. Si vous ne connaissez pas, essayez-les, franchement, ça vaut le détour.
J'ai aussi décapé une bonne partie du casque (maintenant qu'il ne colle plus au touché) car je vais remettre une couche de gelcoat au rouleau plus tard comme sur le 1er casque.
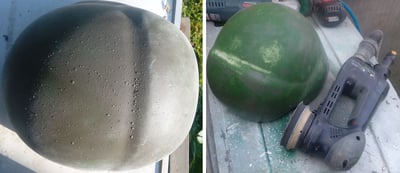
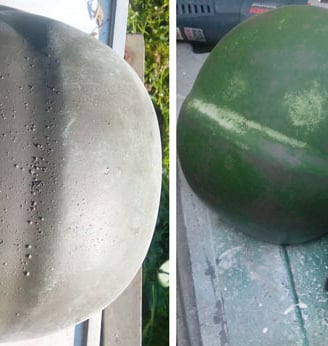
3.1.3- Tests suivants
3-4 tests de gelcoat avec colorant plus tard. Ce que je remarque, c'est qu'il faut absolument mélanger le catalyseur d'abord avec le gelcoat puis seulement après ajouter le colorant. Ce dernier doit empécher le catalyseur de bien se mélanger au gelcoat eta tendance à le laisser collant. Et plus je met de colorant, plus il est collant.
Bon, moi j'ai l'habitude de faire des casques médiévaux en résine. L'imitation métal s’obtient par poudre de graphite et d'aluminium ou autre poudre de métal. C'est simple et ne réagit pas avec le gelcoat. Là, les pigments et les colorants, ce n'est vraiment pas pareil. Ça fonctionne à 3% de catalyseur si j'ajoute le colorant après et en très petite quantité. Sinon même après avec une grosse quantité et 8% de cata, ça reste collant. Les résultats sont trop aléatoires, je pense que je vais acheter directement un mélange spécial résine de pigment couleur vert olive, ça va régler le problème tudju ! Vu que je dois recommander des trucs, autant acheter directement un mélange à la bonne couleur.
3.2- Les ratés
Les tests, c'est justement pour voir ce qui marche ou pas.
Le gelcoat thixotropé dans le moule en guise de 1ère couche, ça ne marche pas, le temps qu'il sèche, j'avais commencé à mettre du mat de verre et j'avais à peine finit de mettre la dernière bande de la 1ère couche que la rétraction du gelcoat avait commencé. Par contre en dernière couche (à l'intérieur du casque) après séchage des stratifiés, vu que c'est devenu solide, ça ne se remarque pas.
La 2ème photo, c'est une réaction du gelcoat coloré à la peinture en bombe. Autant la 1er test de peinture en bombe était encourageant. autant celui-là non. D'une marque de peinture à l'autre, soit ça marche, soit ça merde.
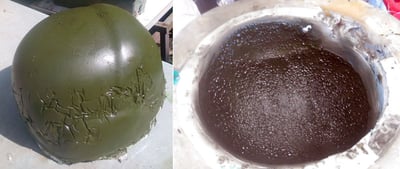
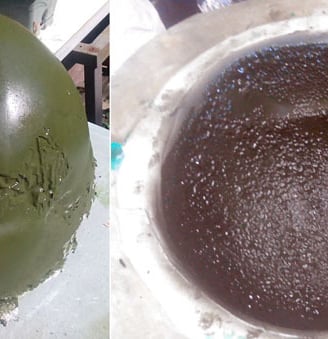
3.3- Tirage en série
Bon, l'achat d'un colorant au RAL 7013 (Ranger Green) fut un fiasco. Et en plus je n'ai pas réussi à le verdir pour l'utiliser. Du coup j'ai utiliser du vert et du rouge et un peu de ce pseudo RG pour faire ma propre couleur.
Pfff, on ne m'y reprendra plus.
Enfin bref, entre la couleur qui ne correspond pas et les problèmes de décollement et de frippage de la 1ère couche (parait que c'est du au fait que l'épaisseur n'est pas uniforme entre autre; enfin bref, je galère bien à produire ce casque. JE mets plus de temps de post traitement que de moulage. L'enfer. Pour éviter les décollement, j'ai même essayé d'appliquer la 1ère couche en 2 fois. 1ère photo, j'ai badigeonner les zones à problèmes et un peu à droite à gauche histoire de ne pas gâcher le surplus de gelcoat fabriqué. Séchage 36h puis le reste de la couche. Reséchage 36h puis je commence la stratification. Le résultat n'est pas parfait non plus. Mais ça marche à peu près. Sauf qu'il me faut 4 jours rien que pour le moulage si je fais ça à chaque fois.
Enfin bref. sinon quand il y a trop de bosses, fils de verre qui dépassent, je laisse durcir un peu plus longtemps entre 2 couches et je ponce avant de faire la strate suivante, afin de limiter l'apparition de bulles.
en parlant de bulles, j'en ai sur ma 1ère couche, il a fallut poncer et reboucher tous les trous avant la finition de la coque. Et ça, sur toutes les coques. Quand j'vous dit que cette 1ère couche me fait suer....
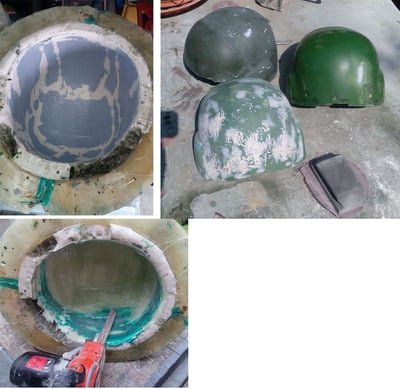
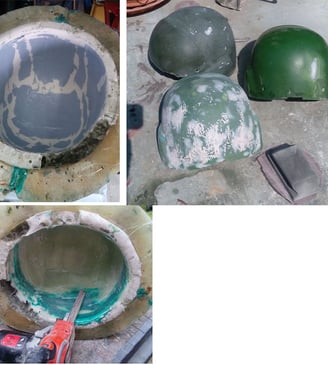
3.4- Perçage
Perçage diamètre 6.5mm pour vis de diamètre 6mm pour les trous du harnais et plus pour l'écrou à souder.
J'utilise un bout de tronc en appuie derrière quand je perce, histoire de ne pas trop éclater la matière en sortie de foret. Un truc que je fait toujours quelque soit la matière: le trou en sortie est plus propre. Et comme avec un casque je ne pouvais mettre une simple planche plate de bois, il a fallut trouver un martyre arrondi à défaut d'être bombé: un bout de tronc d'arbre.
La résine+fibre, comme toutes les matières plastiques, je les perce avec des forets à métaux.
Et enfin un coup d'ébavureur pour adoucir les bords et retirer les bavures comme son nom l'indique. Un petit outil pratique. C'est en gros une lame courbe qui pivote toute seule sur son manche pour tourner dans le trou.
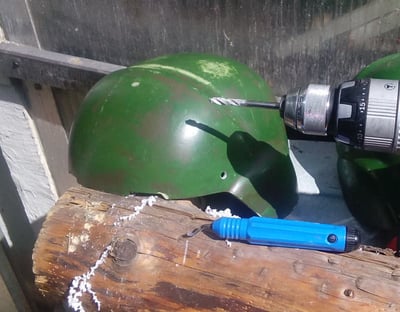
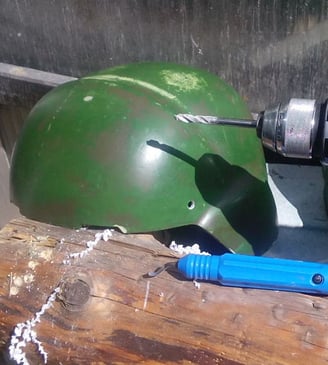
3.5- Dernière couche
NB: voici un tuto sur comment obtenir de la peinture verte:
Avec ça, on a les bases pour savoir faire une nuance de vert particulier, ici une forme de vert olive.
Quand les coques sont prêtes, application de 2 couches de gelcoat teinté au rouleau en mousse pour l'aspect granité. Avec le gelcoat tout frais bien brillant, on voit bien le coté granité sur le reflet du soleil.
NB: vu que je l'applique au rouleau comme une peinture, la couche est très fine, d’où le fait d'appliquer 2 couches. Mais du coup c'est aussi 2 rouleaux mousses de consommés. J'ai donc attendu d'en avoir fait plusieurs avant d'appliquer la couche finale. Ici il y a 7 coques pour cette première série.
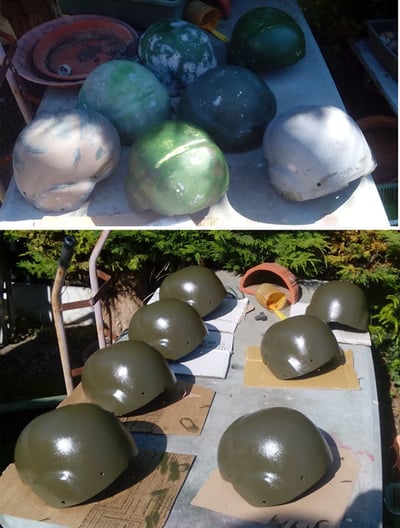
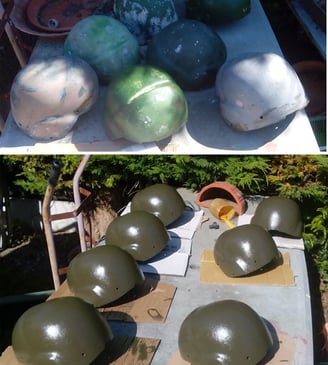
Pour un bien il faudrait que j'applique une couche de vernis semi-Mat par au-dessus, histoire de protéger le tout (vu que la couche verte de gelcoat est fine), mais je pense qu'il y a déjà assez de boulot comme ça. Il faut compter au final 3 jours par casque plus 1 jour pour l'application du vert au rouleau. Et le vernis,il faudrait un bon vrai vernis marin par exemple que j'aurai envie d'appliquer, mais ça coute un rein et 2 yeux ce truc Surtout le vernis souple que j'ai en tête (fonction anti-choc) et qui va consommer un rouleau aussi car c'est une résine non-nettoyable aussi. Bref j'ai pas envie d'ajouter encore 1 jour de taf et 100€ de dépenses supp. Ce sera donc juste une couche de vernis Mat en bombe.
Voilà, les 7 premières coques de félin sont finit.
Avec mes problèmes non résolus de 1ère couche qui merde, ils ne sont pas exempt de défauts malheureusement comme vous pouvez le voir sur les photo. Mais ça passe et le rendu général reste très propre.
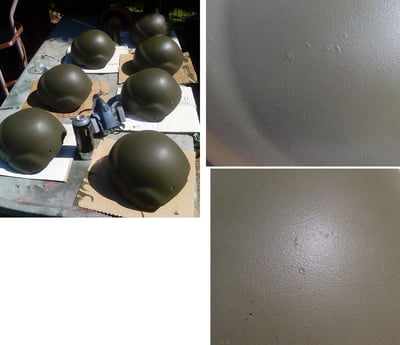
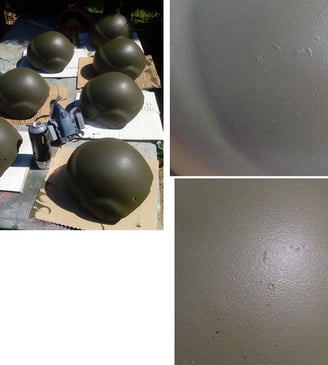