Casque Felin EmersonGear
Fabrication d'un casque Felin sur la base d'un Mich d'airsoft EmersonGear.
CASQUE FELIN - AIRSOFT
Préambule
En airsoft, EmersonGear propose un Mich en ABS. Très léger et facile à trouver.. Je vais partir du modèle OD et l'habiller comme un casque Felin. La forme de la coque ne sera pas la bonne, mais habillé avec les joncs et les plaquettes, ça fera très bien l'affaire pour pas trop cher.
En airsoft, EmersonGear propose un Mich en ABS. Très léger et facile à trouver.. Je vais partir du modèle OD et l'habiller comme un casque Felin. La forme de la coque ne sera pas la bonne, mais habillé avec les joncs et les plaquettes, ça fera très bien l'affaire pour pas trop cher.
NB: la copie de Mich en résine de Mil-Tc n'a pas tout à fait la même forme. du coup ces 2 Mich d'airsoft ne sont pas comptaibles malheureusement.
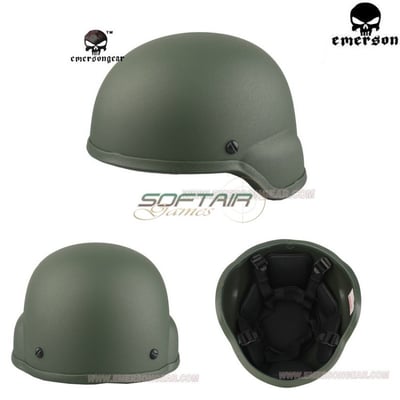
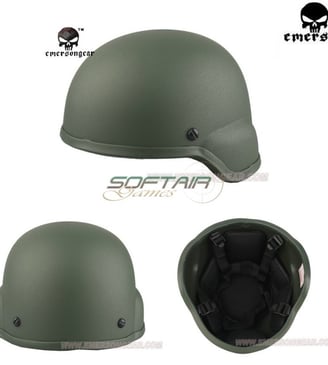
1- SCANNAGE
D'abord, le casque est désossé histoire de ne conserver que la coque pour le scannage. Et une fois la coque nue, j'ai ajouté de la "texture" histoire que le logiciel comprenne bien la forme par photogrammétrie etc...
2021, un nouveau joujou au TechShop de Lille, un scanner 3D.
L'Artec Leo et le logiciel Artec Studio 14.
C'est un scanner à 15-20 kilobrouzouf et un logiciel à 1k/mois, le genre de truc qu'on ne peut pas se payer.
En plus, sans un PC à 3-4GHz, 50Go de mémoire etc etc comme au TechShop, ben ne rêvez pas, ça ne tournera pas vraiment bien chez vous. J'ai installé la démo de la v15 pour voir, mon PC est à la total ramasse.
Ce n'est pas un modèle parfait pour les petits objets comme les casques, mais ça fait quand même l'affaire et donc mon bonheur.
Je m'amuse donc en ce moment à scanner des casques dans le coin studio photo.
Le scannage est intelligent, intuitif et très simple: sur l'écran, la couleur verte, le scan désigne ce qui a été correctement localisé, en orange, les zones à finir car il manque encore des points de repérage et en rouge, les zones de l'objet non fait.
On scanne l'objet à l'endroit, puis à l'envers. J'ai fait au moins 2 scan à l'endroit pour augmenter la précision. Chaque scan fait environ 2à3 Go.
Ça prend 15-20mn à charger sur le PC via le RJ45.
Sur Le logiciel, ça se passe bien, les temps de traitement sont assez long malgré l'énorme config du PC. Je passe 2h minium pour nettoyer les scans et les assembler. Mais une fois fait, le mesh du casque est nickel et déjà à l'échelle. Le plus long, ce sont les temps de calcul et d'enregistrement des fichiers. Par ce qu'un "projet" (un casque avec plusieurs scans), c'est 10Go en moyenne.
Le mesh final est exporté en obj.
C'est un gros fichier, mais je ne vais l'utiliser qu'avec Instant Mesh qui gère les gros fichiers sans broncher, c'est assez impressionnant d'ailleurs.
Instant Mesh est un freeware (téléchargeable sur gifthub), une application qui ne s'installe pas, juste un exe que l'on lance après l'avoir dézippé.
Le fichier obj créé sur Artec Studio est un trimesh (un maillage de triangle donc des faces à 3 cotés). Si vous ne le simplifiez pas, vous verrez que lesdits triangles forment des carrés ou presque. Le fichier non simplifié est donc pas mal d'origine pour être exploitable en quadmesh (maillage en face à 4 cotés, carrés ou rectangles).
Dans InstantMesh, d'abord je sélectionne "quads 4/4". Pour bien lui dire que je veut qu'il me créé un quadmesh à la fin.
Notez (flèche rouge) que la taille du maillage sera d'environ 20k. S'il est plus petit, il interpolera donc pas la peine de grossir le format. PAr contre s'il est plus gros, mieux vaut redescendre autour de 20k (pour ma part en tout cas), sinon l'objet généré sera difficile gérable par Fusion360.
Ensuite, j'ai coché "sharp crease". S'il y a des bords franc sur votre objet, il ne lissera pas le bord mais le rendra tel quel en gros.
On clique sur le 1er "solve", il fait apparaitre comme des traits de peinture, ça indique le sens des quadmesh qu'il va généré.
Puis on clique sur le "solve" suivant et on visualise le maillage quadmesh qui a été généré.
On part donc d'un maillage triangulaire plus ou moins adapté pour la conversion (cf le gros plan de la 1ère image) donc, pour arriver à un maillage quadrangulaire (carrés/rectangles de la dernière image) en quelques clics et quelques secondes. Ce freeware est génial!
Bref on clique sur "exporte", une nouvelle fenêtre apparait.
Là je coche "pure quadmesh", on sait jamais.
Puis on clique "extract mesh" et enfin on sauvegarde ("save").
Et c'est là que tout se joue: si vous exporter en obj comme moi, il faut absolument taper obj nous même à la fin sinon vous aurez un message d'erreur et rien ne sera sauvegarder. C'est con mais c'est comme ça.
NB: par le passé, avec mon ancien windows, je n'avais jamais réussi à sauvegarder et je ne savais pas pourquoi. Là, avec la mise à jour vers le nouveau windows, il veux bien sauvegarder. Aucune idée de pourquoi. Mais en tout cas, ça marche maintenant, donc je peut enfin convertir des maillages trimesh en quadmesh youpee!
A quoi ça sert de convertir en maillage quadmesh? Pour que Fusion360 puisse le convertir en solide. Sinon cela reste un maillage avec toutes les limites que cela implique.
Alors, dans Fusion360, dans "solide", on va aller dans "insert" et on va "insérer un maillage" pour pouvoir importer notre quadmesh tout nouveau tout beau.
NB: parfois le maillage apparait avec un petit triangle d’avertissement. Il suffit de cliquer dessus, l'option "coudre et fermer" par défaut fonctionne bien généralement pour "réparer" le maillage afin qu'il soit parfaitement exploitable.
Puis on va cliquer sur "forme", la modélisation organique. Dans les outils, il y a "utilitaires" et là-dedans, il y a l'option "convertir".
Une fenêtre apparait, on choisit "maillage quadrilatère vers T-spline", on sélectionne la forme et hop, ça calcule, ca calcule... et si tout va bien, on obtient notre objet quadmesh en forme organique (facette à 4 cotés aussi).
Il arrive parfois qu'il plante ici. J'ai parfois utiliser une autre option de réparartion de la forme. Ou j'ai utilisait une autre forme générée par InstantMesh (au lieu de quad 4/4, on sélectionne quad 4/2) par exemple, ou on modifie le sens des traits de peinture....
Mais franchement, en exploitant les bruts d'ArtecStudio au format obj, je n'ai pas eut de soucis du tout.
Reste plus qu'à cliquer sur "Terminer la forme" pour revenir au menu "solide". Là, pareil, il calcule, il calcule... et vous sort forme solide finale et exploitable.
C'est sur ce n'est pas une surface simple et lisse, mais ça reste très précis et c'est suffisamment exploitable pour moi.
NB: pareil, ça peut planter à cette étape parfois. Je fais pareil que décrit précédemment pour y réussir à avoir un solide. Mais là, je n'ai pas eut de soucis non plus avec mes scans Artec.
Donc voilà, j'ai mon scan de casque Mich Emerson convertit en solide sans effort.
De là, j'ai un bon point de départ pour modéliser les plaquettes, les rails...
2- MODELISATION
1èere modélisation.
1ers tests, on voit ou on découpe un peu les bords du casque Emerson.
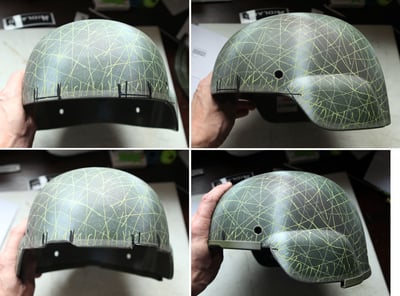
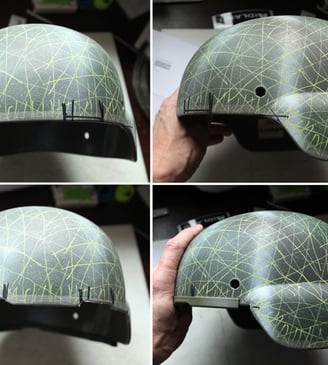
Après 4-5 tests pour ajuster la forme du jonc, j’obtiens un résultat convenable.
Les joncs s'emboitent en forçant, du coup ça tient déjà tout seul sans colle.
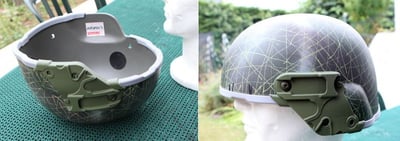
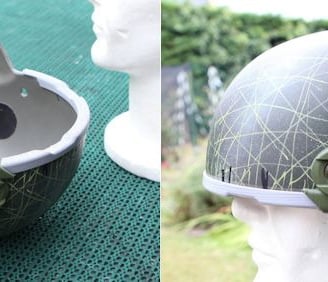
Un coup de peinture sur tout ça. Ici j'ai utilisez un coup de peinture Ranger Green sur la coque et un coup d'Olive Drab sur les joncs & les oreilles. Peinture de chez Fosco Industries.
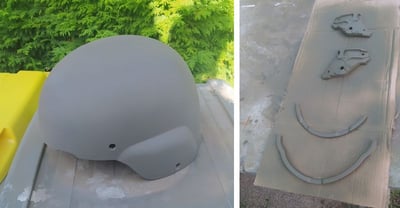
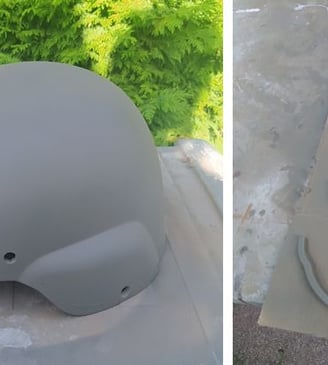
Pour coller les joncs, Sachez que sur le vrai casque, ils ne sont fixé que faiblement... via quelques points de silicone/ colle polymère translucide.
Vous pouvez donc faire de même avec un fond de cartouche de joint de cuisine/salle de bain, ça fera très bien l'affaire. PAs contre ne faites pas comme moi, mettez-en très peu, comme sur le vrai, sinon ça déborde et c'est la galère pour le retirer.
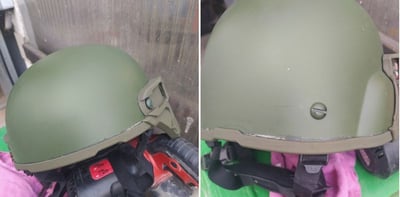
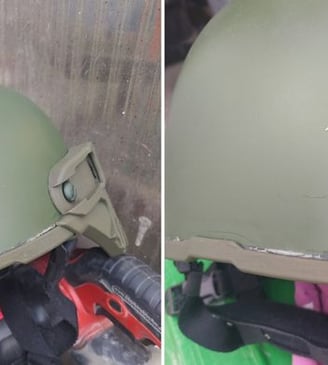
Pour l'habillage intérieur ou la visserie, je vous invite à regarder la page dédiée suivante: Casque Felin maison: 5- Habillage.
En ce qui concerne la visserie de ce pseudo casque Felin, vous aurez besoin de :
2 vis M6x14
4 vis M6x10
2 inserts filetés M6
3- MOULAGE
Cette fois je tente le moulage. Du coup je vais modélisé des modèles positifs pour couler de la résine dans le moule de tirage. Ici c'est le modèle positif pour couler les joncs. La partie bleu sera à couper à la fin mais permet possède une forme évasé un peu comme un entonnoir pour faciliter la coulée.
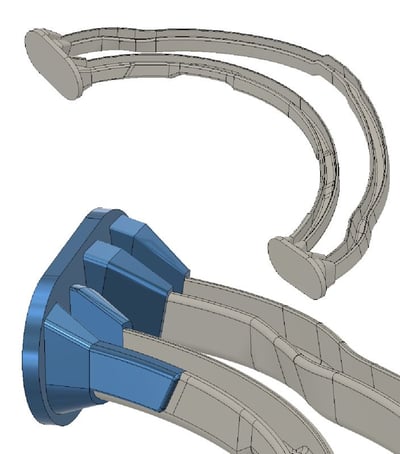
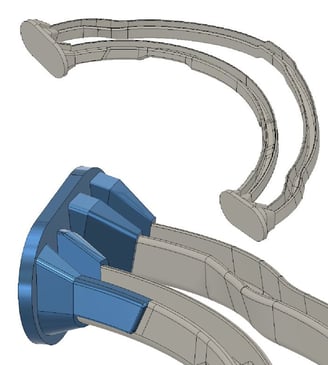
Et ici on peut voir le moule en 2 parties réalisé en élastomère de silicone.
Je coule d'un coté jusqu'à ce que ça remonte de l'autre. La forme permet d'évacuer l'air emprisonné et les bulles qui se forment lors de la réaction chimique.
Ce moule est efficace et j’obtiens des joncs très propres.
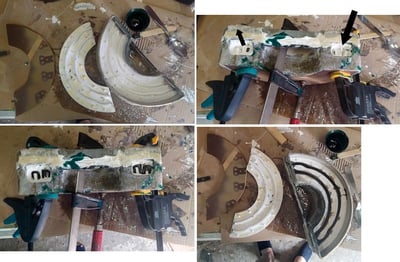
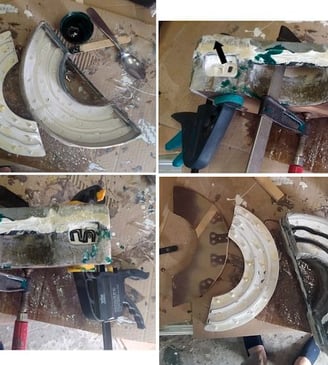
Pour la plaquette, l'aileron pose problème pour le moulage. Du coup j'ai fait une ouverture sous l'aileron (cf les flèches), ça simplifiera le moule de tirage. Et je prévois de faire des puits de chargement, la face avant en bas, la face interne pourra être pleine de bulle de dégazage, ça ne se verra pas du coup. enfin c'était l'idée de départ.
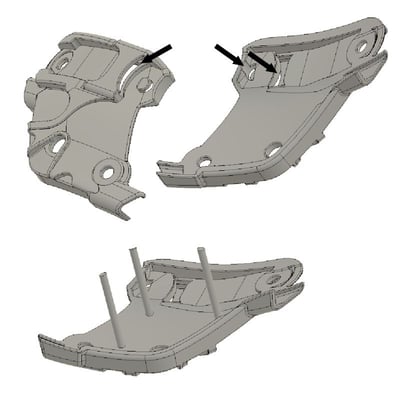
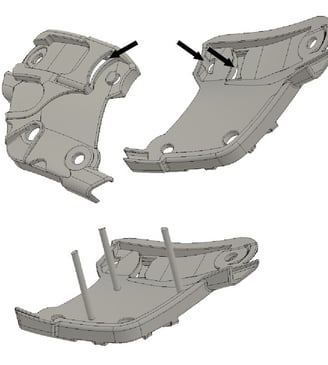
La partie basse du moule en élastomère reste dans une "boite".
La partie haute, vu que l'élastomère risque de se déformer sous le poids par gravité, je prévois que le couvercle soit plein d'aspérité pour retenir l'élastomère en place. Et pour celà, rien de tel que des vis à têtes larges. Je plante un tas de vis dans un bout de bois, et de l'autre je meule les pointes saillantes de vis. Histoire que le couvercle perçé de vis ne pique pas comme un hérisson lorsque je le manipulera.
Ensuite je visse toutes ses vis sur le couvercle.
La partie basse, elle, contient la plaquette dans de la plastiline. Une couche d'alcool polyvinylique (agent démoulant) permettra de couler l'élastomère et de retirer plastiline et plaquette sans que l'élastomère ne soit collé dessus.
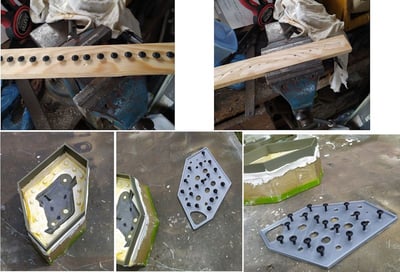
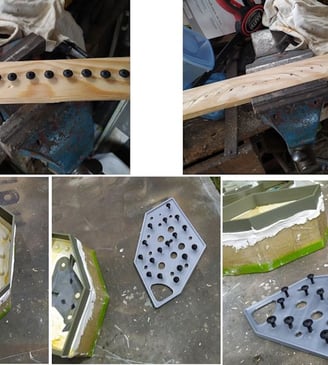
1ère étape, je place le couvercle et coule l'élastomère. Une fois polymérisé (sec), l'élastomère est solidaire du couvercle.
Ensuite on retire la plastiline de la partie basse et on coule l'élastomère dans la partie basse.
On a alors les 2 parties du moule de prête.
Et là je fait mon 1er tirage. Si vous regarder bien c'est un échec. Il manque la partie qui recouvre la tranche du casque. Tout le dégazage se fait dans ces zones.
Raté.
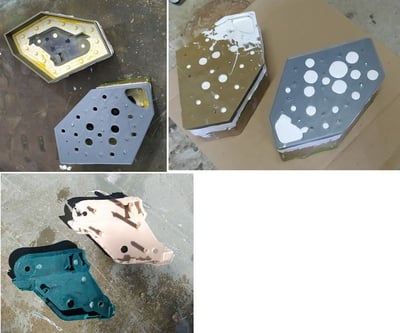
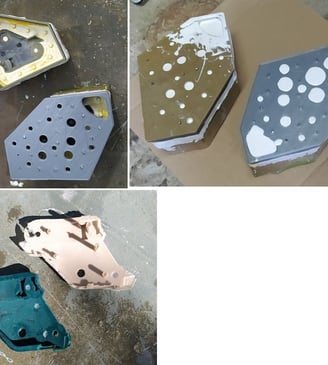
Je change e stratégie. Je rebouche les 3 évents d'origine et je creuse des saignées sur l'arrière de l'élastomère.
Bref je met la pointe avant de la plaquette vers le bas. Et l'arrière de la plaquette muni de saignées vers le haut pour de nouveaux tests de coulage.
C'est mieux mais pas encore parfait.
Bon j'abandonne, ce moule partiera à la poubelle.
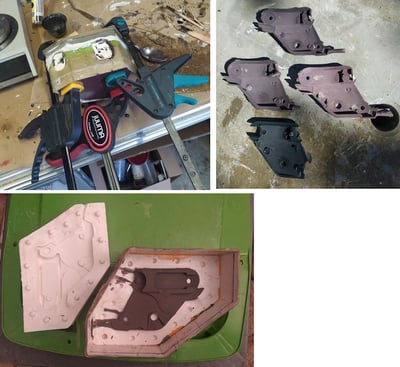

Là ou se faisait encore des dégazages, je creuse de nouvelles saignées. Du coup, je fait un nouveaux moule.
NB: pour connaitre la quantité exacte d'élastomère hors de prix, je remplis d'eau et je mesure ledit volume d'eau. Comme ça je sais de quel volume d'élastomère j'aurai besoin pour faire mon moule.
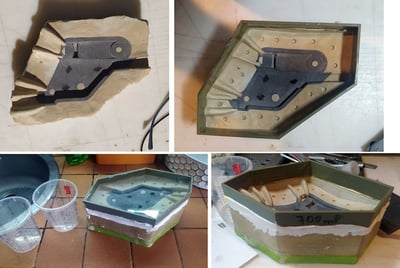
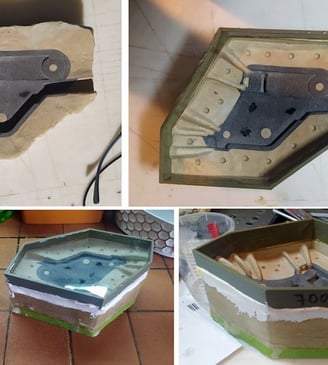
Une fois la partie "basse" du moule faite en élastomère, je retire le fond de la boite pour retirer la plastiline. Et une couche d'agent démoulant avant de passer faire la 2ème partie du moule en élastomère.
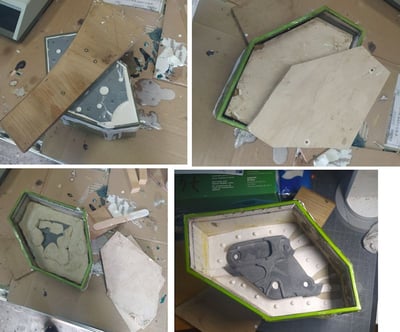
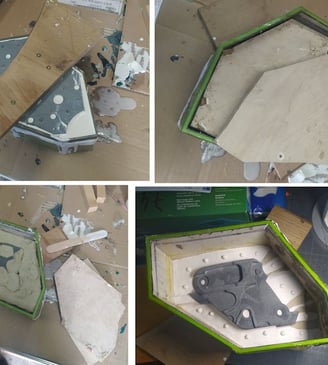
j'en profite d'ailleurs pour créer des ouverture pour que les saignées soient débouchantes et que je puisse couler la résine de tirage des plaquettes.
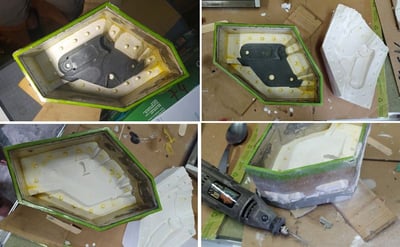
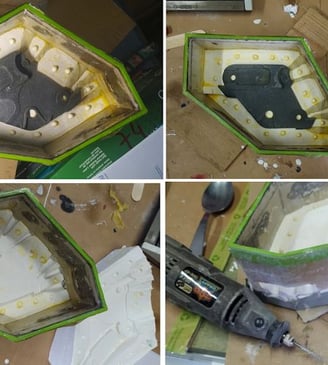
Comme pour les joncs, je coule d'un coté jusqu'à ce que la résine remonte de l'autre.
Cette fois, le teste est concluant. Par contre, si je ne serre pas un peu les 2 parties du moule ensemble, la résine "bave" entre les 2 parties du moules. Ca fait un peu de travail de finition à faire.
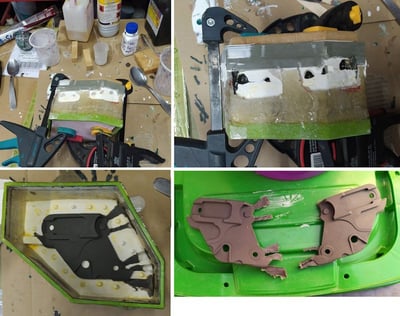
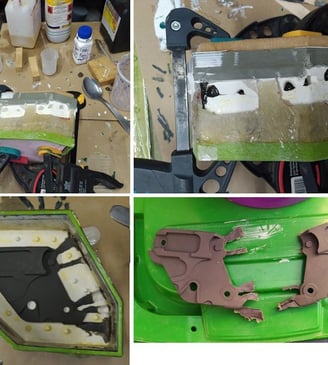
Et voilà, je peux faire quelques kits prêt à l'emploi pour faire des casques Felin EmersonGear
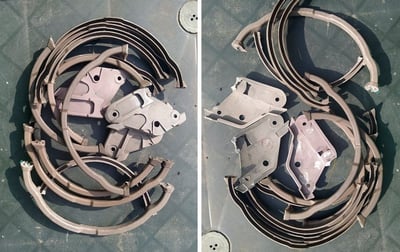

Et voilà, le modèle est terminé. Par moulage, ça a bien plus de gueule qu'une impression 3D amha.
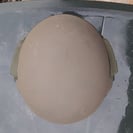
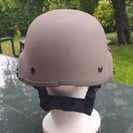
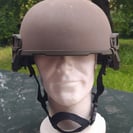
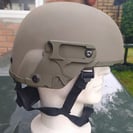